By Tim Botimer
Above: Tim’s International 110 sailboat. After winning the National championships, he gave her a new coat of paint.
I first got into International 110 sailing 15 years ago and soon bought an old fixer-upper boat. After sailing it for a couple of years in a decrepit state, I made the decision to fix it right. I had worked with WEST SYSTEM® products before, and I was pretty familiar with the product line. I had done significant repairs on a 1965 plywood Thunderbird and a 1950s vintage Flying Dutchman, which incidentally was one of the original test boats when Jan and Meade Gougeon first came out with the product. I had never tackled anything on the scale of the 110 project, and at the time it was the only boat I had.
I first got into International 110 sailing 15 years ago and soon bought an old fixer-upper boat. After sailing it for a couple of years in a decrepit state, I made the decision to fix it right. I had worked with WEST SYSTEM® products before, and I was pretty familiar with the product line. I had done significant repairs on a 1965 plywood Thunderbird and a 1950s vintage Flying Dutchman, which incidentally was one of the original test boats when Jan and Meade Gougeon first came out with the product. I had never tackled anything on the scale of the 110 project, and at the time it was the only boat I had.
The International 110 was designed by C. Raymond Hunt, and many are home built. Mine was Number 300, the first one produced by Jesek Brothers boatbuilders of Holland, Michigan. The boat is constructed of 3 8″ Douglas fir marine plywood over Douglas fir frames. The four keel frames are white oak. It sailed in the very first 110 Nationals in 1941.
The boat was showing its age, so the first thing I did was strip off the heavy fiberglass cloth on the hull to see what I really had. I knew I would be putting a new bottom on at the very least, and I wanted to know what I was getting into from the start.
With the glass and paint (at least 10 coats, all of different colors) removed, I found that the sides and the bottom were both dry-rotted along the seams. The bottom frames were still in pretty good shape except that they were the wrong shape. The first eight feet of the bottom was too flat and then there was a two-inch hump where the keel frames were.
I replaced one of the oak keel frames and repaired the others. I found that the ends were rotted where the screws that hold the chine onto the frames went in. I scarfed a new end onto one frame, and I used a Dutchman scarf to repair some rot on another. The frames were just like new.
After replacing all of the bottom frames to give the boat the proper shape, I added stringers fore and aft to give more structural stability between the frames and to prevent the bottom from sagging between the frames, especially where the boat sits on the trailer. The frames and stringers were coated with clear epoxy and then sanded to allow for a mechanical bond. I used stainless screws to hold things in place until the epoxy hit its initial cure, and then I removed all of the screws.
I planked the bottom first and then repeated the process on the sides. Using marine grade 3 8″ Douglas fir plywood, I used a special tool to cut a 7 to 1 scarf to join the plywood and make a continuous 24′ piece. The plans call for a butt joint; however, with the bottom ply scarfed, the boat drains better. I used WEST SYSTEM 105 Resin with 206 Slow Hardener. I wet out the joint with straight resin/hardener, and then I mixed up a batch with 403 Microfibers for gap filling. I clamped the plywood together, and the resulting joint hardly shows and is stronger than the original wood.
Putting the bottom and sides on was a three-person job. I had two people mixing resin/hardener and adding 406 Colloidal Silica and 403 Microfibers. They would mix up about a 5-pump batch from the mini pumps and then add the fillers. The mix was then loaded into the handy reusable caulk gun tubes and applied to the frames and stringers.
Once the whole thing was glued and screwed, all three of us climbed in and scraped the excess epoxy off all of the surfaces where it had squeezed out. Using the stir sticks, we formed fillets with the excess epoxy. This was quick and easy, and it made a much stronger joint.
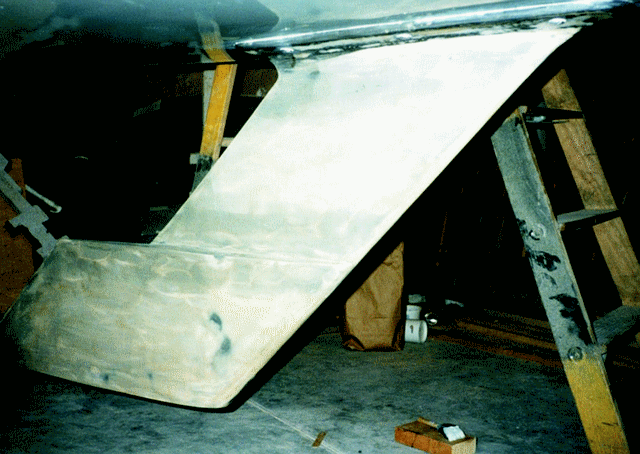
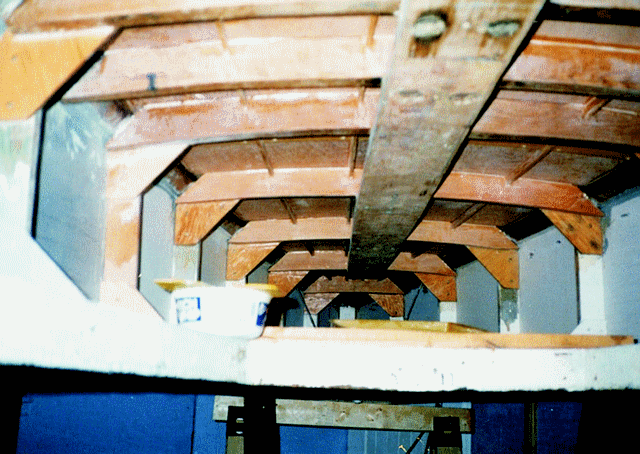
To fair the hull, I used WEST SYSTEM 105 Resin/205 Fast Hardener thickened to a thick peanut butter consistency with 410 Microlight®. I also used this mixture extensively to reshape the keel to the correct shape. Once the shape was achieved, I coated everything with several coats of the 105/205 epoxy/422 Barrier Coat Additive.
The keel is cast iron and very prone to rust weeping through. I wire wheeled the keel clean of rust and then wire brushed epoxy barrier coat onto the keel. I rolled the glue on and then wire brushed it into the pores of the cast. The next four coats were just rolled on one after another as soon as they were hard enough to take another coat.
WEST SYSTEM Epoxy worked equally well for finishing off the exterior of the hull. The interior got three coats of clear epoxy and then varnish. The exterior got seven coats of epoxy mixed with 422 Barrier Coat Additive. This stuff worked great because it made sanding and seeing imperfections easier. It also made the surface much more impervious to water. The exterior is finished with Interlux™, Interthane Plus™ two-part polyester paint, applied with a roller and tipped out with a good brush.
International™ 110 Number 300 had a new lease on life. This rebuild was done in 1994, and I haven’t had to do any major touch-ups to the boat. In 2003, after winning the National championships, I gave her a new coat of paint. I have since done several other 110 rebuilds and have learned a few tricks and tips to make the job easier. Planning sure beats sanding is probably the biggest lesson learned. I now use Okoume mahogany plywood instead of the Douglas fir. It is much more dimensionally stable. I also call the WEST SYSTEM Technical Services when I have a question instead of trying to figure it out on my own. The folks at WEST SYSTEM are very knowledgeable and always willing to help.