Why reinforce with carbon fiber?
By Don Gutzmer
Carbon fiber has very high strength-to-weight ratios and higher stiffness compared to many other reinforcing fabrics. These special properties make it ideal for applications in aerospace, automotive, military, and even sporting goods. When combined with a WEST SYSTEM Epoxy it can be used to build high-end composite parts.
Although carbon fiber is one of the strongest and most lightweight materials used in the composite industry, the expense can make it cost-prohibitive. To achieve the same look of a carbon part without the cost, a process called skinning/wrapping can be used.
Carbon fiber skinning is often done cosmetically, where the look of carbon fiber is desired but the strength (and expense) of a true carbon composite is not necessary. A part manufactured from a less expensive reinforcing fabric is “skinned” with carbon fiber. It’s a popular look on motorcycle parts, car interior panels, and mirrors. In addition to the standard reinforcing fabrics, there are eye-catching hybrid fabrics that are a blend of carbon fiber, Kevlar™, and glass that come in a variety of colors. There are so many different choices of fabrics on the market now, there’s one to suit most everyone’s needs.
For my project, the use of carbon fiber was to take advantage of its cosmetic appeal. I decided to wrap the fiberglass air scoop for my boat motor with one layer of 5.8 oz. plain weave carbon fiber.
The scoop was originally painted orange, so I needed to make the surface black before applying the carbon to avoid any orange paint from showing through the weave of the fabric. The first step was to sand the painted scoop well before applying WEST SYSTEM® 105 Resin and 207 Special Clear Hardener, which was tinted black with 502 Black Pigment. Because this is not a structural application it is acceptable to bond to a well sanded painted surface. The following day I sanded the cured surface dull with 120-grit sandpaper.
The next step was applying the carbon fiber to the scoop. A light mist of spray tack (3M Super 77) held the carbon cloth on the surface and prevented the fabric from distorting and moving. Using too much spray tack can cause adhesion issues, so I used only a little. The cloth was then ready to be coated with 105 Resin/207 Hardener. I wet out the carbon with epoxy then applied multiple light fill coats of 105 Resin/207 Hardener to provide a high-quality clear finish. I applied these coats every 3-4 hours with a bristle brush to prevent the epoxy from running.
After the epoxy cured it was wet sanded in preparation for a UV protective topcoat.
I had many different topcoats to choose from, but I wanted to keep it simple so I sprayed a couple coats of lacquer to provide the smooth high gloss finish. I’d say the project was a success and turned out looking pretty nice on the motor.
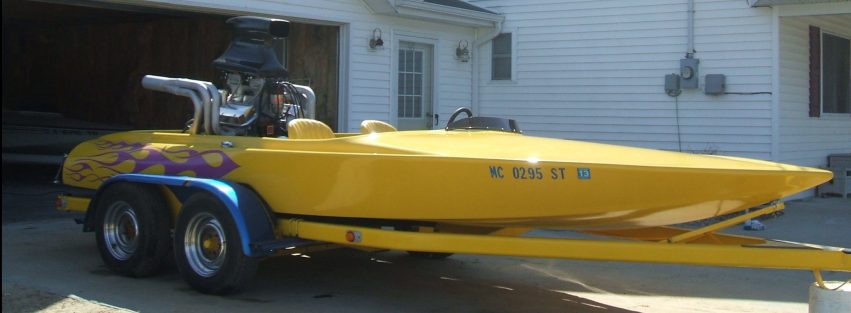