Editor’s note: This article was originally written in 1994, long before we developed G/flex epoxies which offer vastly superior performance in bonding to plastics including PVC. A much more current article on this subject is Gluing Plastic with G/flex Epoxy by Tom Pawlak and Jeff Wright. If you’re interested in gluing PVC with epoxy, we suggest you start there. The following article is published at Epoxyworks.com for historical purposes only.
by Brian Knight—GBI Technical Advisor
Occasionally our customers ask about using WEST SYSTEM® Epoxy to bond PVC (polyvinyl chloride) plastic to another surface. Typically, traditional epoxy doesn’t adhere well to many plastics due to a lack of surface texture for a mechanical bond. With some plastics, the epoxy forms beads on the surface like water on a waxed finish. This lack of ability to “wet out” the surface is another reason for poor adhesion.
But with proper surface preparation, it is possible to achieve excellent adhesion to many plastics. Since the preparation varies from plastic to plastic, I tried various surface preparations on the PVC in an attempt to find one that will work well with WEST SYSTEM 105 Resin-based Epoxy.
In order to know how well epoxy sticks to PVC, I used the PATTI (Pneumatic Adhesion Tensile Testing Instrument) meter. This test instrument measures the amount of pressure necessary to remove “pull-stubs” from a substrate. In this case, the pull-stubs were bonded to a flat PVC panel using WEST SYSTEM 105 Resin and 205 Fast Hardener.
The chart below shows the various methods used to prepare the PVC surface prior to bonding the pull-stubs. As you can see, two methods yielded good results.
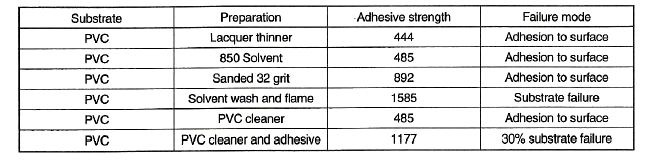
PVC cleaner and PVC adhesive
Of the two methods that provided the best results, the easiest preparation involved the use of standard PVC cleaner and adhesive. These materials are available anywhere PVC plumbing supplies are sold.
First I cleaned the plastic surface with PVC cleaner and then applied a thin film of PVC adhesive and wiped off the excess. The PVC adhesive acts as a primer for WEST SYSTEM Epoxy, greatly enhancing its adhesion to this plastic. Be sure to use a very thin film of the PVC adhesive and let it dry to the touch before applying the epoxy.
Flame oxidation
The flame oxidation method involves removing any surface contamination with a solvent and then heating the surface with a propane torch. (Note: use caution with an open flame near a solvent. Many solvents are highly flammable so be sure all traces of solvent on the plastic surface have evaporated. Remove the solvent container from the work area before using the propane torch. Work in a well ventilated area.) If done correctly, the open flame heats the surface of the plastic without melting it. This thermally oxidizes the surface of the PVC, allowing the epoxy to chemically adhere to it. With proper lighting, you can see the gloss of the PVC surface change as the flame passes over it. It will become slightly less shiny. Play the flame quickly over the surface making sure that the flame contacts the entire surface. Do not allow the plastic to melt. This method yields the best results using the PATTI meter, but it is the most difficult method with which to achieve consistent results. It also is impractical for large surfaces.
Using either method outlined above, you can bond PVC sheet plastic or PVC pipe to any substrate that is compatible with WEST SYSTEM Epoxy.