An option in boat construction or repair?
By Bruce Niederer — GBI Technical Advisor
Wood has always been used in fiberglass boat construction, in stringers, and oftentimes as core in high compression areas such as under cleats, stanchions, and winches. Wood works great in these applications but we all know that the big problem with wood is the fact that it rots if it gets wet. Here at Gougeon Brothers, Inc. (GBI), we have spent long hours writing manuals and training people to use proper techniques using epoxy to keep wood dry and strong.
But wouldn’t it be nice if it simply didn’t rot?
This is the idea behind some testing I conducted to learn whether or not Azek PVC deck boards would be a viable substitute for wood in select situations.
First, I considered density because it seemed a bit heavy—but with a quick bit of online research, I learned that wasn’t the case. The density of Azek PVC is definitely in the ballpark. (See density chart below.)
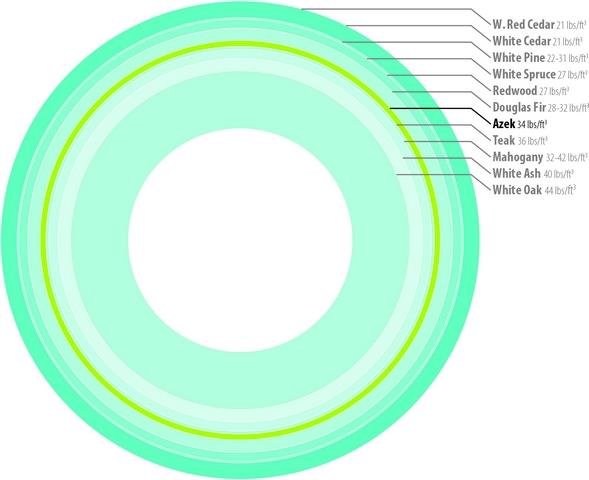
Now it was time to look at adhesion. I used two surface preparations; 1. Sanding with 60 grit using a random orbital sander and 2. A flame treatment (reference “Gluing Plastic with G/flex” in Epoxyworks 26) and two epoxy systems; 1. WEST SYSTEM 105 Resin/206 Slow Hardener, and 2. G/flex 650.
In the tensile adhesion data to the right, there’s nothing unusual in the results for the sanded surface—I expected G/flex to perform somewhat better than the 105/206 system. Although the average tensile adhesion values are very similar (within about 100 psi) the failure mode reveals quite a bit more substrate failure using G/flex.
The flame-treated surface tells a different story. All 20 test sites—regardless of what epoxy was used—failed 100 percent of the Azek PVC, creating large voids in the surface. The epoxy did not fail, and the average adhesive strength was identical.
The hardware removal—pull-out test, is again very revealing. The average pull-out strength of the fastener threaded into a proper pilot hole is 761 lbs of direct load (the upside-down numbers on the bottom of the samples). The numbers are very closely grouped indicating the value represents the shear strength of the Azek PVC with that particular thread. Adding a little 105/206 into the pilot hole and painting some on the fastener threads changed the failure mode from a shear failure to a destructive failure, breaking the PVC out in chunks. This raised the pullout strength by 389 lbs.
All of these data sets—density, adhesion, and hardware bonding support the notion that the Azek PVC copolymer PVC deck boards may well be an option in certain boat building and repair applications. Clearly, it can be substituted for wood backers and crush-resistant core applications i.e.: under stanchions and loaded hardware. One final consideration is the cost—one ¾” x 6″ x 12′ Azek PVC board purchased locally costs $46. That’s probably not a deal-breaker but it’s something to keep in mind.