By Bruce Niederer — GBI Technical Advisor
The beauty of a wooden boat is undeniable. It doesn’t matter whether it’s sail or power. When I see one, my response is both cerebral and primal, and I know I’m not alone. I began racing sailboats in the late 1970’s and, without exception, it has always been aboard FRP production boats. In 1980, I was invited to crew on my first long distance race, hosted by the Buffalo Yacht Club near the northern end of Lake Erie. The afternoon before the race the harbor was full of plastic racing sailboats. Their crews, all hard-core sailors, were busy making the usual last minute preparations for the next day’s race. The quiet of the harbor was slowly disturbed as a vintage triple cockpit barrel back mahogany runabout idled in, the sound from the exhaust a hint of the power hidden within. As the skipper, a gray-haired gentleman wearing a Greek fisherman’s hat, motored amongst us to check things out, an amazing thing happened. One by one, boat by boat, everyone stopped what he or she was doing and moved to get a better view of this magnificent craft. In itself, this may not be so amazing, but what happened next certainly was. Every sailor in the harbor broke into spontaneous applause! The skipper graciously tipped his hat and smiled broadly. Piloting his boat outside the breakwall, he throttled her up and made a couple of passes, roaring past the harbor to t
he delight of us all. Such is the appeal of these marvelous wooden watercraft.
Many people who build or restore boats like that one should be considered artists and historians as well as fine craftsmen. The history of Bay City, Michigan, boasts a diverse legacy of boat building and maritime tradition that includes war ships built for WW2 and the presidential yacht Sequoia built at Defoe shipyard; world class racing sailboats and DN ice boat champions built by Gougeon Brothers; and both Gold Cup and Unlimited Hydroplane champions as well as classic mahogany masterpieces known worldwide. Doug Morin, owner of Morin Boat Works, has witnessed, created, and documented much of Bay City’s maritime history and continues this tradition of fine craftsmanship and mahogany artistry today. With over 600 restoration projects completed to date, Morin and his crew have earned a well deserved reputation as one of the best restoration boathouses in North America for antique and collectable classics. Their boats have consistently won Best of Show awards across North America.
I first met Doug about 3 years ago when I helped escort students attending the boat repair school here at GBI on a tour of his facilities. We entered an unassuming building with so many additions it’s hard to say where the first section begins or ends. Doug was spreading out some photos and news clippings of pieces he has restored or built new, as well as some his father was involved with. I’ve come to realize since that first visit that Doug, while very proud of the work he does, prefers to frame his success in the context of his family and their contributions to the history and rich boat building traditions mentioned above, rather than just pat his own back. When he talks to the group, he begins with something like “My father began working for Les Staudacher in 1947 and became a project manager building cruisers, runabouts, commuters, Gold Cup Racers and later Unlimited Hydros. All with wood, of course, and epoxy eventually. My brother and I helped and learned when we could and then started building and racing small outboard hydroplanes for about 15 years and then another 5 or 6 years with inboards. We got into restoring old mahogany Chris Crafts and Hackers little by little after that. So I guess I’ve never had a real job in my life!” That may be true, but he has spent more hours of his life with a piece of sandpaper in his hand than any other ten people I know put together, and I call that work.
The first phase of any restoration project involves a thorough investigation into the history of the piece. Establishing and documenting the authenticity or pedigree of a boat is as integral to its value, when the project is complete, as the restoration itself. Doug has attended shows where identical boats have shown up, oddly enough, with the same hull ID numbers! When something like this happens, the value of both boats is dramatically reduced. Consequently, Doug is meticulous in his research and has developed an impressive network of sources all over the world from which to draw. Simply stated, he is a walking encyclopedia of boat building history, covering everything from builders and past owners to hull construction, materials, hardware, and engines.
Controversies surrounding materials and techniques employed in a restoration and the historical impact of one vs. another have plagued the restoration community for years. In Morin’s opinion, debating issues such as which type of adhesive to use—epoxy or sealant/adhesives—in a historically significant piece is really a non-issue. He feels, and we at GBI concur, that for a boat to be considered historically correct, modern adhesives of any type cannot be employed because they didn’t exist at the time of construction. In fact, many museums would rather leave a piece as is when it is found, preferring only to authenticate and document its history prior to its new life as a museum piece. Other than that, virtually nothing used in a restoration, from adhesives and fasteners to the type and quality of woods (especially mahogany) and varnishes available today can be considered original.
That said, each restoration project must be approached holistically. Doug’s philosophy is to select and use materials that will make the boat better than originally built while maintaining the original dimensions, lines and appearance of the piece. When doing a restoration, he utilizes an arsenal of techniques gained over a lifetime of boat building. This includes a judicious and technically correct use of WEST SYSTEM® epoxy that is dictated by the project, the piece, and the range of use the boat is really likely to encounter in its lifetime. The success of his work over some 30 years and the number of satisfied, repeat customers who are willing to spend a great deal of money for each project stand as testament to his philosophy, technique, and results. Currently, Morin has about five restoration projects underway in the shop: a 26′ Riva, a 28′ Garwood, a 30′ Hacker, and two Gold Cup Racers including My Darling (photo), a 1949 multi-step Unlimited Hydroplane that will be powered with an Allison aircraft engine. This is a sister ship to a racer built by his father at Staudacher’s named My Sweetie. Generally speaking, restoring a racer or a unique one-off like My Darling is somewhat easier to plan because it is not usually shown in classes quite as embroiled in the controversies mentioned earlier.
In addition to restorations, Doug has designed and built seven new, runabout style boats, each reflecting a different influence or period. Each piece is unique and will never be duplicated at his shop, so current owners are assured of the long-term value of their investment. New boats are not restricted by material selection considerations the way restorations are, so each of these boats, while reflecting the influence of classic designs, is completely built using modern materials and techniques. They are stunningly beautiful examples of a marriage between the old world and new technology. New boats are generally framed, then skinned with Okoume plywood and planked with mahogany. One exception to this approach is the Morin 21 Speedster (photo) whose design reflects the influence of a prewar racer with painted sides instead of planking.
Doug uses WEST SYSTEM epoxy throughout the construction of these new boats. All end grain is well coated, whether exposed or not. All wood to wood unions are bonded with epoxy, including the plywood to the frames and the mahogany planking to the plywood. Most fasteners are used only as clamps until the glue cures, and are then removed and the holes bunged. Those left in place, in high load areas, are countersunk and bunged. Structural or load bearing hardware is mounted using the same hardware bonding technique advocated here at GBI. To address moisture exclusion, the bottom and any surface below the waterline receive 3–5 coats of epoxy. Freeboard and deck areas get 2–4 applications. Hard to reach places such as the underside of the deck get 1 or 2 coats.
Doug knows that epoxy doesn’t make a boat completely maintenance or worry free. However, he views epoxy as an effective tool among many he might choose from, saying he “values the support system provided by the technical staff and consistent quality of WEST SYSTEM products.” Improper care, particularly poor ventilation while not in use, can turn any well-built boat into something else, and this is a situation he has little patience for. The success and longevity of literally hundreds of Morin restorations, as well as Morin’s new boats, have created a lasting legacy to be proud of. Pieces from Morin Boat Works can be found from California to New Hampshire to Canada. All of us at Gougeon Brothers are proud to be associated with Doug and his crew. They represent, and are committed to, what we consider to be the very best in boat building craftsmanship and artistry.
Editor’s note: This series began with Mahogany Masters I – Van Dam Custom Boats.
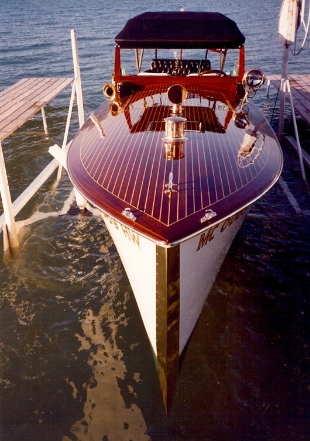