Lesson 2 in our series on Strip Planking
by Ted Moores
At the La Routa Maya canoe race in Belize, SA., we saw a natural progression from chopping canoes out of logs to fiberglassing strip-planked boats with WEST SYSTEM® Epoxy. Strip-planking may have been the first step after the dugout in the evolution of boatbuilding techniques; the way the quality of wood is going, it might be the last to survive. With our strip-planked hull faired and the outside stem attached, there are many techniques that could turn these strips into a boat.
Building the depth of a dugout canoe using pegs or edge-nailing narrow planks is universal. The Belizean builders take strip-planking to the limit by building most and sometimes all of the hull with edge-nailed strips and even using strip-planking to replace the rotten end of a large dug-out.
When we add technology like fiberglassing with epoxy to this primitive way of building, wood becomes an engineering material and the possibilities get very interesting.
In the race, the Dory class or dug-out canoe class is popular and competitive. The hulls are chopped and shaped from a large softwood log to a thickness of about one-half inch. Then fiberglassed on both sides with polyester resin. In 2000, we introduced fiberglassed strip-plank canoes to the race. The following year, there was a canoe with carved ends and a strip-planked mid-section with everything glassed on both sides. The builder later came to visit to learn how we build the ends without the chopping.
At this year’s race there were about a dozen strip-planked/WEST SYSTEM Epoxy canoes built from our molds. Since Maagga Ting, the third boat we built, proved to be an excellent design for this challenging four-day race, the boats are now built in-country using Kevlar™ and carbon fiber. Of the 75 canoes in the race, about twenty of them were Maagga Ting clones that were first-place finishers in most of the classes.
Using strip-planking as a foundation for multiple layers of veneer is an excellent building method, especially if the hull is to be bright finished.
When I considered the number of steps and materials involved in fairing the strip-planking, applying two or more layers of veneer, fairing the hull two or more times, fiberglassing the finished hull for durability and then hiding it all under paint, my question was “What are all those layers of veneer really doing?” The way I see it, we have fibers crossing the strip-planking on the diagonal to tie the longitudinal planking together and spread the strong wood fibers in a number of calculated directions.
Looking for the best results with the fewest steps, the question was, “Why not eliminate all the veneering steps and use all glass fibers?” One of my principles in designing a composite hull is to create a balanced panel. Applying the same amount of glass to both sides of a strip-plank core is a simple way of building a balanced, core-composite panel.
The next question was “How much fiberglass would it take to replace the fiber strength of the veneer?” The 30′ C15 sprint racing canoes we build have an average crew weight of 2,300 lb, so we knew what one layer of 6 oz glass on ¼” planking could do. Sparks (Epoxyworks 32), with a displacement of 6,800 lb, was beyond a wild guess in terms of reinforcement and there was no data I could find.
Outside of keeping up the paint, the hull is one part of our boat that I don’t want to have to revisit. To get it right, we needed numbers. The Gougeon Test Lab generously offered to do the testing. Based on the results of these tests, we came up with a lay-up schedule for fiberglassing strip-planked hulls that optimized the amount of reinforcement.
Did we get it right? During our test cruise last summer, we broadsided the end of a jetty. A quick check for damage showed no structural damage to the hull. A scientific measure of how hard we hit would be interesting; a guess is difficult as we were distracted by visions of being sucked over the dam and certain death. One indication is the 7/8” ash trim compressed to about half of its original thickness at point of contact.
“Think Lazy” or the shortest route to the best results
Ending up with a fair hull was high on my list of priorities. Each step, beginning with CNC router cut station molds, had to be a step in that direction and prepare for the next step rather than being a cycle of damage control between steps. Assuming that the mold is fair, executing each step consistently over the whole surface should produce a fair surface. Controlling the thickness of each layer of glass as it is applied eliminates most of the sanding needed to fair an irregular, casual lay-up.
Fiberglassing Strip-Planked Boats Using WEST SYSTEM Epoxy
Lay-up schedule: Before installing the keel and skeg, we applied three layers of 6 oz × 60″ wide glass cloth on the diagonal in alternating directions and running from sheer to sheer. Applying the glass cloth on the diagonal doubles the number of glass fibers crossing the longitudinal wood fibers.
Testing showed a significant increase in stiffness and impact resistance without additional material or weight. The bonus was that at 45°, the cloth easily wrapped around the stem and followed the complex shape of the fantail.
Staggering the joints on a number of layers of lightweight glass meant that the edges of the cloth could be butted. This eliminated the need to overlap the edges of the glass and then wait for the epoxy to cure enough to feather the joint before we could proceed. Glassing could continue as soon as the epoxy was firm enough to work on, and we were sure of a good bond between layers.
The trick to controlling the thickness of each layer of glass and epoxy is to know what each step is meant to accomplish and have a visual reference for the ideal amount of epoxy. When you know what it should look like, simply make all of the surfaces look the same. To get the best bond between layers and keep the hull fair, we saturated each layer of glass until the shape of the cloth was distinct without being starved. Starved, or too little epoxy will show as a whitish glitter. Excess epoxy will look shiny, indicating that the glass is floating in a puddle. If left to harden, these puddles will either have to be sanded fair—with a good chance of damaging the glass fibers—or they’ll become another wave in your hull.
Our Three-Step System
Step 1—First layer of glass over dry wood. The purpose is to saturate the surface of the wood and the fiberglass.
What to look for and why: Achieving a consistent amount of epoxy in the cloth calls for more than just carefully applying the epoxy. Each plank will absorb a different amount of epoxy, so it’s important to apply enough to feed them all. As the epoxy soaks in, the wood fibers become saturated and the space between the fibers is filled. This increases the density of the surface and the epoxy makes a deep mechanical bond inside the wood.
The wicking action of the cloth is the key to drawing the air out of the wood and feeding the epoxy in. When any finish is applied over bare wood, the film wants to break over any void. It then pulls back and piles up around the edge, much like over-filling a glass of beer. The surface fibers will become saturated but it is hard to work the epoxy into the wood and force the air out. When coating plywood without fiberglass, it takes multiple coats of epoxy with aggressive sanding between coats to eliminate the pin holes and completely level the surface.
To apply epoxy to fiberglass cloth, simply transfer the epoxy from the container and gently spread it over the cloth. Don’t work it into the cloth; the cloth will do a good job of feeding the wood at the speed it can absorb the epoxy, and less air will be introduced. On horizontal surfaces, a small puddle can be pored on and moved about with the squeegee or a roller. Both of these tools excel at spreading thin, consistent amounts of material so expect to apply a number of coats before the wood stops absorbing the epoxy.
I use a brush to coat strip-planking to spread large but controlled amounts of epoxy quickly. The trick is, don’t even try to make it look good at this point. As long as it is not looking dry, break any big bubbles but don’t waste time on the small ones for now, just keep moving on. When the excess is removed with the squeegee, you can expect it to look good.
Using WEST SYSTEM 105 Resin® and 207 Special Clear Hardener®, we wait about 20 minutes for the wood to have a good drink before removing the excess epoxy, brush hairs, and bubbles using a squeegee. The trick here is to hold the squeegee at a low angle to avoid removing too much epoxy thus starving the cloth. Expect to do a number of passes before you reach the picture you are looking for; the cloth should be in the same shape as when dry but look saturated with no whitish glitter (too little epoxy) or shiny puddles (too much epoxy). Dispose of the excess epoxy by dragging the squeegee through a 3/4″ slit in a heavy paper cup or cardboard frozen juice can. It is important to keep the same time between applying the epoxy and removing the excess. If the excess is removed too soon, the wood could continue to draw the epoxy out of the cloth, leaving it starved.
Removing all the excess epoxy with a squeegee before it cures eliminates a lot of sanding and cleanup, and the surface remains fair. No effort should be made to build up the thickness of epoxy until all the glass is on.
Building layers of cloth
While it is possible to build up multiple layers of glass at a time, we changed directions with each layer on Sparks and staggered the joints so the logistics for multiple layers didn’t work here.
If you were to saturate a second layer of cloth now that there is a stable base to build on, a more predictable and lesser amount of epoxy may be applied using a roller, squeegee, or brush. Apply it to a manageable area then go back over it with the squeegee to remove any excess, looking for the even, saturated fabric texture.
The optimum time to re-coat is when the last coat is just firm enough to work on without disturbing it. (About five hours with 105 Resin/207 Special Clear Hardener.) To do this, each coat must be made in preparation for the next because at this stage, the epoxy is too green to remove runs, etc. This will reduce the possibility of surface contamination and result in the best bond between layers.
Build up coats
Step 2—Second coat. The purpose is to level the weave of the cloth.
This textured surface will be coarse enough that air may get trapped in the weave when the next coat of epoxy is applied. To avoid this, we apply this coat with a squeegee. The objective is to pack the epoxy in and force the air out, leaving a surface that is closer to smooth. After packing it in, go back and scrape off the excess epoxy. Work systematically, again looking for a consistent texture.
Step 3—Third and subsequent coats. The purpose is to bury the cloth for durability and have something to sand off later.
I am comfortable with two more coats applied with a roller and tipped off with a bristle brush. Because each coat has been applied consistently, the final sanding will not need to remove very much epoxy to achieve a smooth surface.
Installing the keel and skeg
The keel and skeg were glued on over the three continuous layers of glass and tied in with three more layers extending from the top of the keel to the waterline. This doubled the number of layers on top of the keel and put the edge to be feathered where it would show the least.
Masking tape follows a waterline scribed into the wood before glassing to show the area to be wet out with epoxy. The extra dry cloth keeps the brush away from the fuzzy cut edge. When the epoxy reached the green stage, we sliced under the glass with a sharp chisel held at a low angle, cutting it cleanly along the taped line. Carbon fiber was used to prevent the laminated skeg from expanding and to tie it into the bottom. This was the dusty part of the job as the thickness of the carbon fiber required considerable fairing with epoxy thickened with 410 Microlight® filler to make it disappear.
After we feathered the edge of the glass along the waterline, the shape was fair again.
We buried the fiberglass under one coat of 105 Resin/207 Special Clear Hardener applied with a squeegee to level the weave. We followed that with two coats applied with a foam roller and tipped off with a brush. Going from this epoxy surface to an incredibly fair hull ready for paint was a simple matter of consistently cutting the gloss over the whole surface.
Fiberglassing the inside
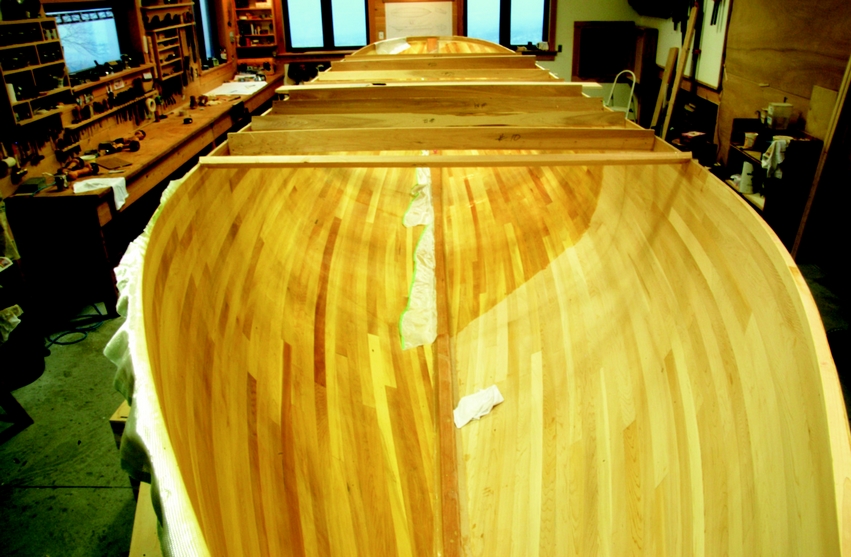
Before fiberglassing strip planking on the inside, the edge of the hull needed to be stabilized in the designed shape. In spite of drying the wood and then letting it come up to average shop moisture content, the project went from late summer into winter and a heated shop. The hull shrunk a little after glassing the outside, causing the sides to curl in slightly. Spacers, the length determined from the plans, were kept in place while we applied the first two layers. This stabilized the hull in the designed shape. To simplify working inside this very awkward shape, we overlapped the fiberglass ends on top of the keelson by the next layer from the other side. A generous fillet along the edge of the keelson and the glass crossing at 45° allowed the glass to change direction without trapping air in the corners.
To keep the project moving and still work clean, we alternated the application of fiberglass sections to leave some working room and keep out of the sticky stuff. Ideally, I would like to apply the same amount of reinforcement to both sides to keep the panel balanced. Since we have three layers above the waterline and six below on the outside, we split the difference and used four full layers on the inside.
After applying the fourth layer of glass we added one layer of epoxy and used a squeegee to level the weave, followed by two coats rolled on and tipped off to bury the glass. We find that 105/207 has excellent leveling properties so that brush marks flow out and disappear. Runs are not a problem even with the thickest coat if the epoxy is worked into a consistent film thickness.
Working so that each step is preparation for the next might feel inefficient and frustratingly slow for some builders, but adding up all the things you won’t have to undo, and the quality of the results, it could be worth the effort. Doing damage control is usually the task builders learn to hate. When everything you are putting on is becoming part of the boat, there is instant gratification and a measurable feeling of accomplishment. You know that when you have finished putting it on, it is a positive step towards getting her out of the shop and into the water.
Next time we will look at building a skeg that won’t split, a foam core rudder, a low tech rollover jig and a few more cheap tricks.
See Lesson 1 of the SPARKS series—Strip Planking
See Lesson 3 of the SPARKS series—Skeg Construction
See Lesson 4 of the SPARKS series—Sealing and Priming
Related article—Ted’s Jewel Box